Passé la négociation commerciale, la qualité de service vue par le client est directement liée à la livraison à date du bon produit, à la juste quantité et au niveau de qualité attendu. A ce titre, deux indicateurs sont particulièrement surveillés : Le taux de service (ou OTD, ou OTIF) et le nombre de réclamations pour non-qualité. Deux indicateurs simples qui suffisent cependant à qualifier le niveau de performance du processus industriel d’une entreprise. Améliorer la performance industrielle nécessite une approche méthodique en s’appuyant sur les acteurs de terrain.
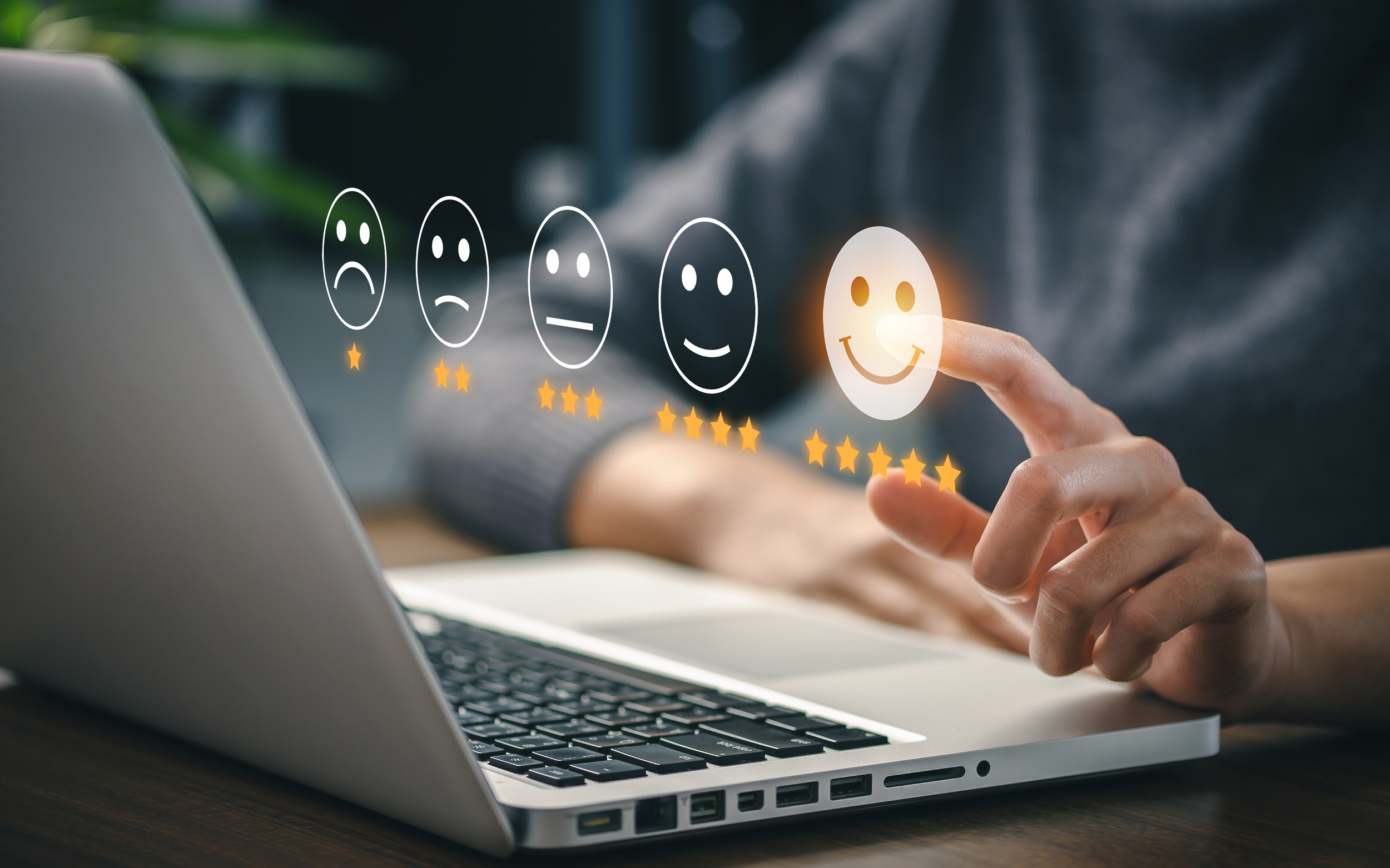
Les défis et enjeux
La fiabilisation du parc d’équipements est un axe majeur qui permettra de stabiliser le processus en réduisant la variabilité de la production que ce soit sur les aspects quantitatifs ou qualitatifs.
Une démarche de fiabilisation permet ainsi d’améliorer la satisfaction globale du client tout en réduisant le coût des opérations (OPEX) par une meilleure utilisation des actifs. Les gains peuvent être rapides par une première étape de fiabilisation ciblée sur les processus de production qui génèrent le plus de perturbations.
Sur le moyen et long terme une stratégie de fiabilisation des équipements permettra de prolonger la durée de vie des équipements et permettra de réduire les investissements de renouvellement (CAPEX).
Bénéfices pour les clients
- Amélioration du taux de service (OTIF, OTD),
- Amélioration de la qualité livrée (réclamations),
- Amélioration de la capacité de réponse (lead time).
Bénéfices internes
- Réduction de la variabilité de production,
- Stabilisation de la planification,
- Stabilisation puis augmentation de la capacité,
- Réduction des risques sécurité,
- Réduction des coûts de non-qualité (CONQ),
- Réduction des coûts de transports exceptionnels,
- Réduction des heures travaillées non planifiées,
- Augmentation de l’efficience et du rendement des équipements,
- Augmentation de la durée de vie des équipements.
Les principes clés
Il est premièrement nécessaire d’impliquer tous les acteurs du processus de production pour identifier les équipements prioritaires sur les enjeux Sécurité, Qualité, Délais, Coûts à différents horizons :
- Horizon court terme
- Horizon 1 an
- Horizon 2 ans et plus
Ensuite, il faut identifier les sources de variabilité (5M) et améliorer le taux de rendement des équipements (TRS).
Organiser les opérations de maintenance est également un principe clé indispensable.
Enfin, l’entreprise doit répartir les rôles et responsabilités entre service maintenance et production pour une approche durable.
Le digital peut apporter de nombreuses possibilités pour améliorer la situation :
- Outils de GMAO : Les logiciels sont nombreux dont certains accessibles en version Web et très simples d’utilisation pour gérer vos machines, documents et interventions associés.
- IIOT (Industrial Internet Of Things) : Ajout de capteurs intelligents qui vous permettront de capter les données opérationnelles pour mieux comprendre votre niveau de performance et les gains potentiels atteignables.
- Outil de Business Intelligence : Pour restituer des données issues de votre système type ERP ou tracking machine.
- Outil de pilotage d’atelier type MES ou Animation à Intervalles Courts digitalisées et interfacées avec vos données.
Les phases
En s’appuyant sur les principes de la TPM (Total Productive Maintenance), une approche pas à pas permettra de construire une démarche solide, adaptée au niveau de maturité de l’entreprise sur chacune des thématiques.
La première étape de la démarche consiste à effectuer un diagnostic suivant trois axes (Pilotage, Priorisation, Exécution) qui permettra de partager les constats et de construire une feuille de route.
Pilotage
- Stratégie de maintenance
- Rôles et responsabilités
- Système de pilotage
Priorisation
- Sécurité des équipements
- Priorités équipements
- Fiabilisation ciblée
Exécution
- Planification maintenance
- Stocks maintenance
- Préparation interventions
- Interventions
- Rebouclage performance
- Contrôle des coûts
- GMAO
- Intégration nouveaux moyens
Les facteurs clés de succès
Le premier facteur clé de succès qu’on identifie consiste à s’appuyer sur une démarche volontariste de la direction et des différents responsables dans le cadre plus global de l’amélioration continue de la performance.
La fiabilité et la variabilité des équipements est multi factorielle suivant le principe des 5M (méthode, moyens, matière, main d’œuvre, milieu). Cela signifie que le sujet dépasse les seuls acteurs de la maintenance et de la production. Les acteurs tels que les planificateurs, les services industrialisation, outillages, achats, contrôle de gestion, ressources humaines devront être impliqués à différentes phases de la démarche.
Collecter des informations précises sur l’état de fonctionnement des équipements est strictement nécessaire. En l’absence d’indicateur TRS (Taux de Rendement Synthétique) d’un équipement, il est nécessaire d’organiser la collecte des données utiles à son calcul en expliquant aux utilisateurs de l’équipement le sens de la démarche.
Il est également très important d’entrer rapidement dans l’action en conduisant les premiers chantiers pilotes de fiabilisation suivant les étapes du DMAIC (Définir, Mesurer, Analyser, Innover, Contrôler) et en utilisant les outils de la résolution de problème. Au besoin et suivant le type de processus (processus à paramètres), il peut être pertinent d’utiliser les outils statistiques du 6 Sigma.
Pour finir, il ne faut pas oublier de valider les résultats obtenus et suivre un plan de déploiement.
> Voir notre cas client Lauener