Afin d’étayer nos propos, prenons le cas d’une mission que nous avons réalisée dans une PME industrielle de 80 personnes du secteur aéronautique.Nous essaierons dans cet article de montrer comment il est possible de valoriser les gains obtenus lors de chantiers Kaizen et de mettre en place une réelle dynamique entre les différents départements de l’entreprise. Il s’agit notamment de rompre avec les méthodes traditionnelles de valorisation de stock, de calcul de coût unitaire standard, d’allocation des frais de structures, du suivi individuel de la MOD et du taux d’utilisation des équipements.
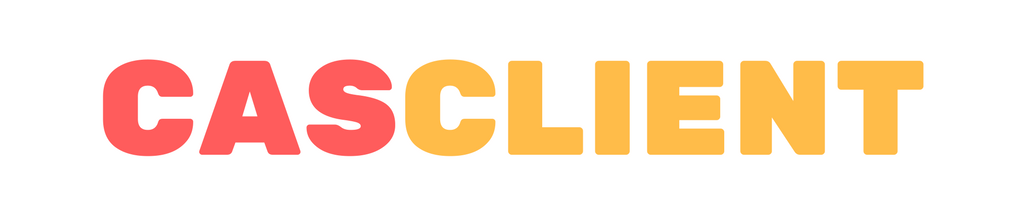
Cette entreprise avait initié, dans le cadre d’un projet d’entreprise, une démarche de Lean Management au sein de ses départements Manufacturing & Supply Chain. Des résultats opérationnels significatifs avaient été obtenus mais la direction financière du site souhaitait mettre à profit cette expérience afin de rendre son processus de gestion « Lean compatible » en investiguant notamment les approches liées au Lean Accounting.
Fort de cette demande, nous avons mené un diagnostic du processus de gestion en place puis avons proposé de déployer la méthode, en collaboration avec les financiers et les équipes opérationnelles.
Tout d’abord, l’analyse et le retraitement du compte de résultat de l’entreprise ont permis de clairement identifier la value stream costing, c'est-à-dire la valorisation de tous les coûts fixes et variables directement imputables à chaque value stream, tout en nous assurant que la somme des charges affectées par value stream était identique au total des charge du compte de résultat.
En effet, afin d’être cohérent et de s’assurer de l’exhaustivité et de la fiabilité des chiffres, il est fondamental de toujours reboucler les calculs avec le compte de résultat global de l’entreprise afin de s’assurer qu’il ne manque pas de charges.
Cette étape, indispensable dans le cadre d’une telle démarche, permet notamment d’identifier les coûts cachés dus aux pertes et à la non-valeur ajoutée par grandes familles de dépenses (matière, énergie, main d’œuvre, structure, …) et permet également d’élaborer le compte de résultat selon les principes du Lean Accounting, c'est-à-dire simplifié, directement exploitable et diffusé à toutes les équipes opérationnelles.
Toujours en collaboration avec les opérationnels, nous avons ensuite identifié les indicateurs pertinents à intégrer dans les « box score » (voir illustration ci-dessous). En effet, il s’agit bien là de construire en équipe, de manière collective, les éléments qui serviront au pilotage de la performance en y intégrant des aspects opérationnels (Lead Time, FPY, Capacité, …) et des aspects financiers (Productivité, …).
Il est important de mentionner ici que le choix de tel ou tel indicateur revêt un caractère particulièrement important au regard des décisions qui devront être prises durant le suivi des activités quotidiennes. À titre d’exemple, on peut citer les innombrables rapports d’analyse de variance reçus mensuellement par les directeurs de production/site. Que fait-on d’un écart d’utilisation équipement, d’efficience MOD, d’absorption des frais généraux, de prix matière, … ?
Le fait d’avoir un taux d’utilisation plus faible peut signifier que la production s’est simplement alignée au Takt time (ou que l'on a réduit les pertes de changement d'outil ou de pièce non conformes), on a moins produit car la demande client a peut-être baissé ponctuellement et il était inutile de faire du stock (espace et coût de stockage, BFR, obsolescence, …).
Par la suite, à chaque mise en place d’un chantier Lean, nous avons alors été capable de chiffrer les améliorations de processus ou d’activité dans les value stream, en isolant les coûts de non-valeur ajoutée.
Cette identification ayant été faite, il nous était alors possible de valoriser les retours sur investissement des efforts fournis par les opérationnels lors de la mise en place du Lean management et de valoriser ainsi les gains que l’entreprise allait obtenir dû à la réduction des temps de traversée, au gain de place, à la libération des capacités machines, à l’amélioration de la productivité et de la qualité.
Cela s’est traduit soit par des gains à court terme, qui se sont rapidement retrouvés dans le résultat net de l’entreprise, soit par des gains à moyen ou long terme.
Le directeur financier a reconnu que seule cette « nouvelle » approche avait permis de faire une telle analyse et, qu’au-delà de ses propres méthodes de gestion traditionnelle qu’il conserverait pour d’autres utilisations, il déciderait d’instaurer cette nouvelle façon d’opérer de manière permanente.
Son système d’information comptable permettant l’extraction des données du compte de résultat sous Excel, il nous a donc été relativement facile de créer un outil simple, rapide et personnalisé afin de « faire vivre » les calculs avec les opérationnels de manière facilitée.
Au-delà des aspects purement technique et/ou financier de la mission, nous avons pu constater la mise en place d’une réelle synergie entre les équipes. Cela a permis également de monter en compétence les collaborateurs des services Finance et Manufacturing dans des domaines qu’ils maîtrisaient moins.
Enfin, nous conclurons cet article en évoquant le sujet, parfois plus délicat à aborder, de la transparence et de la communication autour des gains obtenus qui engendrent souvent des discussions liées aux demandes de contrepartie aux gains réalisés. Ce dernier point peut constituer en effet un réel frein à la conduite du changement.
« Les coûts n’existent pas pour être calculés. Les coûts existent pour être réduits », Taiichi Ohno
Pour en savoir plus :
- Visionnez le replay de la web-conférence sur le Lean Accounting ainsi que les slides sur Slideshare.
- Découvrez le programme de formation Lean Accounting.
Pour aller plus loin et échanger sur vos projets, n'hésitez pas à nous contacter.